In modern manufacturing, precision, durability, and weight reduction are critical factors that determine product performance and efficiency. CNC (Computer Numerical Control) aluminum parts have gained immense popularity across various industries due to their unique combination of lightweight properties and exceptional strength. These parts are extensively used in aerospace, automotive, electronics, medical, and industrial applications where performance and reliability are paramount.
This article explores the importance of CNC aluminum parts, highlighting their benefits, manufacturing process, and key applications in different industries.
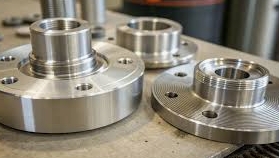
The Advantages of CNC Aluminum Parts
1. Lightweight Yet Strong
One of the primary reasons CNC aluminum parts are favored in manufacturing is their lightweight nature. Aluminum is significantly lighter than materials like steel or brass while maintaining excellent strength-to-weight ratios. This makes it an ideal choice for industries such as aerospace and automotive, where reducing weight directly improves fuel efficiency, speed, and overall performance.
Despite being lightweight, aluminum retains impressive structural integrity, ensuring durability under high-stress conditions. This balance between weight and strength makes it a preferred material for engineers and manufacturers alike.
2. Corrosion Resistance
Aluminum naturally forms a thin oxide layer when exposed to air, providing a built-in resistance to corrosion. This property eliminates the need for additional coatings or treatments in many applications, making CNC aluminum parts ideal for environments exposed to moisture, chemicals, or extreme temperatures. Industries such as marine and medical rely on this corrosion-resistant feature to ensure the longevity of their components.
3. High Machinability and Precision
Aluminum is known for its excellent machinability, meaning it can be precisely cut, shaped, and drilled with minimal wear on cutting tools. CNC machining allows manufacturers to achieve intricate designs with tight tolerances, ensuring consistent quality across production batches.
Additionally, CNC machining provides exceptional repeatability, which is crucial for applications requiring uniformity and precision, such as aerospace components or intricate medical devices.
4. Cost-Effective Production
Compared to other metals like titanium or stainless steel, aluminum is more cost-effective to machine and manufacture. The material's excellent machinability reduces production time, lowers tool wear, and minimizes energy consumption during the machining process. This translates to reduced manufacturing costs without compromising quality.
Moreover, aluminum is widely available, ensuring stable supply chains and predictable pricing, making it a viable option for both large-scale production and custom machining projects.
5. Excellent Thermal and Electrical Conductivity
CNC aluminum parts are widely used in electronics and electrical applications due to their high thermal and electrical conductivity. Aluminum efficiently dissipates heat, making it an ideal choice for heat sinks, electronic enclosures, and components that require effective heat management.
Furthermore, aluminum's conductivity properties make it an excellent alternative to copper in electrical applications, offering cost savings while maintaining efficient performance.
The CNC Machining Process for Aluminum Parts
CNC machining involves using computer-controlled tools to cut, drill, and shape aluminum into precise components. The process typically includes the following steps:
1. Designing the Component
Before machining begins, engineers use CAD (Computer-Aided Design) software to create a detailed digital model of the aluminum part. This design includes specifications such as dimensions, tolerances, and surface finishes.
2. Programming the CNC Machine
Once the design is finalized, CAM (Computer-Aided Manufacturing) software is used to generate tool paths and machining instructions. These instructions guide the CNC machine on how to cut, mill, and drill the aluminum workpiece.
3. Material Selection and Preparation
Manufacturers select the appropriate aluminum alloy based on the part's application and performance requirements. Popular aluminum alloys for CNC machining include:
6061 Aluminum – Versatile and commonly used for aerospace, automotive, and structural applications.
7075 Aluminum – High-strength alloy often used in aerospace and military applications.
5052 Aluminum – Known for excellent corrosion resistance, commonly used in marine and chemical applications.
4. Machining the Part
CNC machines use various tools such as end mills, drills, and lathes to shape the aluminum workpiece into the desired form. The process ensures high precision, with tolerances as tight as ±0.001 inches, depending on the application.
5. Finishing and Surface Treatment
Once machining is complete, aluminum parts undergo finishing processes such as:
Anodizing – Enhances corrosion resistance and aesthetic appearance.
Powder Coating – Provides a durable, protective layer.
Polishing – Improves surface smoothness and aesthetics.
These finishing techniques enhance the part's functionality, durability, and overall quality.
Key Applications of CNC Aluminum Parts
1. Aerospace Industry
The aerospace sector heavily relies on CNC aluminum parts for aircraft structures, engine components, and lightweight frames. The material’s strength, corrosion resistance, and weight savings contribute to improved fuel efficiency and overall flight performance.
2. Automotive Industry
CNC aluminum parts are widely used in automotive manufacturing, including engine blocks, transmission housings, brake components, and suspension systems. Their lightweight properties enhance vehicle speed, fuel economy, and handling.
3. Electronics and Electrical Applications
Due to its excellent conductivity and heat dissipation properties, aluminum is used for electronic enclosures, heat sinks, and connectors. CNC machining ensures these components meet precise specifications for optimal performance.
4. Medical Equipment and Devices
CNC aluminum parts play a crucial role in the medical industry, where precision and hygiene are essential. They are used in surgical instruments, imaging devices, and diagnostic equipment due to their non-corrosive and biocompatible properties.
5. Industrial Machinery
In industrial settings, aluminum CNC parts are used for machine frames, robotic arms, and mechanical components. Their durability and ease of machining make them ideal for heavy-duty applications.
6. Marine and Defense Applications
The corrosion resistance of aluminum makes it a preferred material in marine and defense applications. CNC-machined aluminum parts are used in shipbuilding, military vehicles, and protective enclosures for sensitive equipment.
CNC aluminum parts have become essential components across multiple industries due to their lightweight nature, durability, corrosion resistance, and high precision. The combination of cost-effectiveness and superior mechanical properties makes aluminum a preferred material for applications where strength and efficiency are crucial.
As CNC machining technology continues to evolve, manufacturers will benefit from even greater precision, faster production times, and improved material utilization.
Whether for aerospace, automotive, medical, or industrial use, CNC aluminum parts play a vital role in modern engineering and manufacturing, ensuring high-performance and reliable solutions.
About AJL Machining:
AJL Machining is a professional and industry-leading one-stop workshop for custom metal parts services. We have our own factory and a reliable network of partners that enable us to cater to your requirements ranging from prototypes to large-scale production. Our competitive edge is our ability to ensure that all of your parts are produced according to specifications, within budget, and delivered on time to meet your evolving demands. Presently, we serve over 80% of our business to multinational corporations in China, as well as overseas customers.
To learn more, please don't hesitate to contact us via email at sales@ajlmachining.com, or visit our website at www.ajlmachining.com